Leveraging Alternative Delivery in Emergency Repair Situations
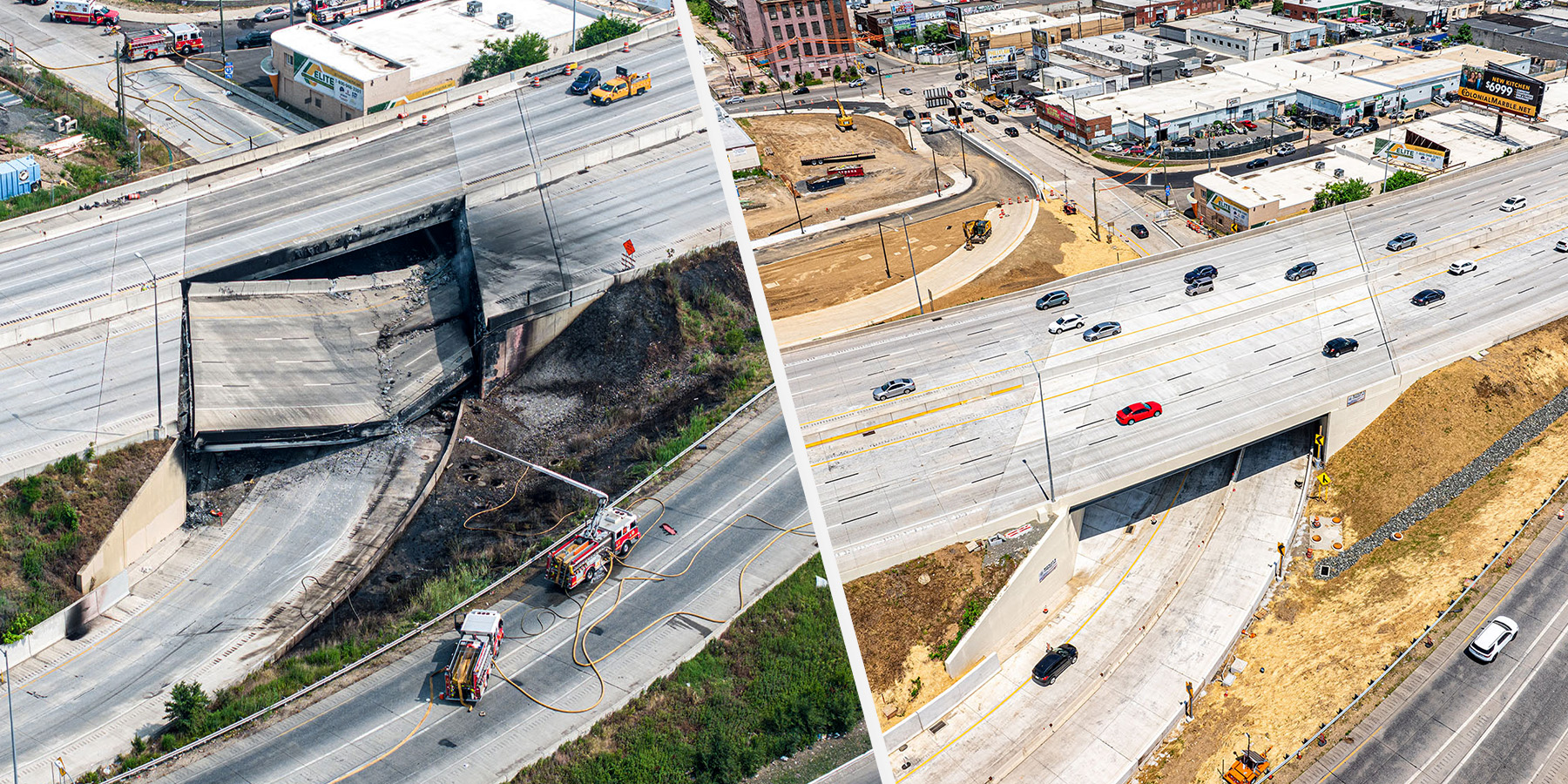
Part 1 – Accident Response
Offering enticing benefits to project owners, it’s no surprise that agencies are increasingly looking to implement alternative delivery methods on a wide range of projects. For emergency repair and replacement projects in particular, these methods have proven to be advantageous.
In this two-part series, Benesch’s Director of Alternative Delivery George Horas provides insight into the benefits of leveraging alternative delivery in emergency repair situations. First up, George explores how a design-build delivery method was used to efficiently replace a portion of I-95 damaged by a truck crash.
Meet Our Expert
Understanding the Draw of Alternative Delivery Methods
In transportation, alternative delivery became widespread post-2008, when the economic recession triggered initiatives like the American Recovery and Reinvestment Act that accelerated projects to stimulate the recovery. The Design-Build Institute of America (DBIA) now forecasts that almost half of all infrastructure construction will be delivered in some form of an alternative delivery fashion by 2026.
For years, Benesch has successfully utilized alternative delivery methods to streamline project execution, ensuring efficiency, cost-effectiveness and flexibility. Recently, these approaches have proven especially valuable in emergency response projects, where rapid mobilization and adaptive problem-solving are critical. While the benefits of alternative delivery are extensive, three stand out during emergency response projects.
Benefit #1: Facilitates Quick Collaboration
The traditional design-bid-build method has the tendency to build silos. While that may not be a problem for planned projects, the success of emergency repair and replacement projects hinge on collaboration.
By integrating key stakeholders—designers, contractors and sometimes even regulatory agencies—almost immediately, open communication is encouraged and expected. As a unified team, we can get a handle on the emergency together and align project goals, optimize designs for constructability and proactively address challenges before they become costly delays. In addition to traditional stakeholders, material suppliers, subcontractors and other parties integral to the construction cycle become immediately available to accelerate decision making.
Benefit #2: Promotes Innovative Problem Solving
With increased collaboration comes increased innovation. Working together from the start allows the design team and the contractor to explore new materials, construction techniques and technologies that might be constrained in traditional delivery models. We’re also able to adapt in real time to find smarter ways to meet our goals. This dynamic approach drives continuous improvement and leads to infrastructure that is not only built faster but also performs better over the long term.
Benefit #3: Saves Valuable Time
When it comes to emergency repair/replacement projects, time is of the essence. Every second needs to be spent wisely to get the impacted infrastructure back in service as quickly as possible. Alternative delivery methods streamline project phases and allow work to progress concurrently rather than sequentially. This minimizes downtime, accelerates decision-making and reduces constructability issues. Additionally, the increased collaboration enables the design team and contractor to more quickly address any unforeseen complications.
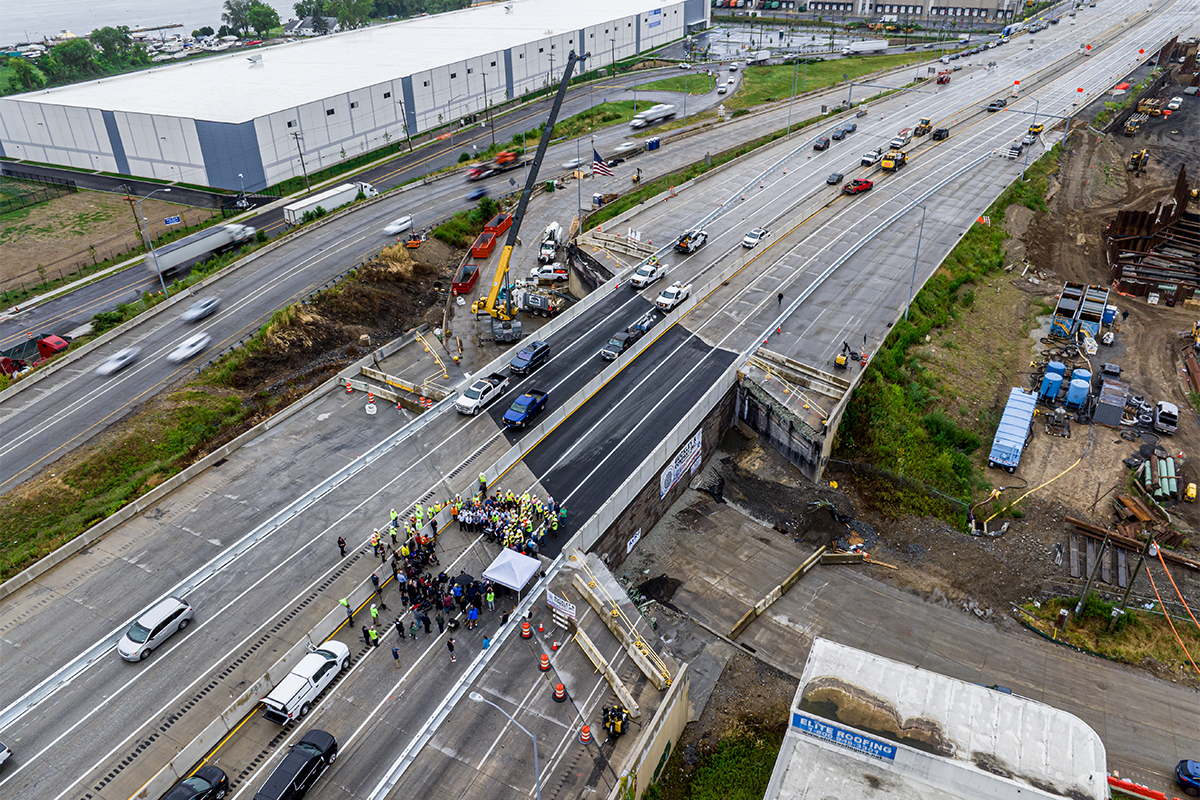
Case Study: I-95 over Cottman Avenue
Reopening a critical section of I-95 in Philadelphia after a fire-induced collapse of the northbound structure required an agile design team and a design-build delivery approach. Utilizing innovative materials such as lightweight foamed glass aggregate fill, precast barriers, and a temporary geogrid wire wall retaining system allowed for a temporary roadway to be constructed. Just 12 days after the collapse, three lanes of traffic in each direction were restored as construction continued on the permanent replacement bridge. Because of an Emergency Declaration, a Sole Source Design Build Delivery Method was chosen. The State used this delivery method on the Fern Rock Bridge collapse in Pittsburgh in early 2022.
The Benesch Team started design work for the permanent bridge replacement in the days after the collapse. Critical staging limit decisions were made within hours of the collapse so the temporary roadway and permanent bridge replacement solutions could work together. Leveraging a design-build delivery method allowed the team to tailor the updated steel bridge design for efficient fabrication and construction.
Construction of the first phase of the permanent bridge was completed in November of 2023. Once traffic was shifted to the permanent bridge, the temporary roadway was demolished, with some components transported to other sites for reuse. Construction of the second phase was completed in the summer of 2024 just one year after the accident. If conventional delivery had been chosen in response to this situation, it would have taken months for a temporary solution to be decided upon and implemented followed by a permanent bridge two years later.
Benesch continues to employ alternative delivery methods to accelerate project timelines, coordinate seamlessly with stakeholders and deliver high-quality solutions under urgent conditions. Our experience has shown that alternative delivery not only enhances responsiveness but leads to more resilient and sustainable infrastructure solutions.
In part two of this series, George will explore how the use of alternative delivery methods can be beneficial when a natural disaster strikes. Follow Benesch on LinkedIn for first access to future insights.